Packaging Machine Repair Service: Ensuring Marginal Downtime and Optimum Effectiveness
Comprehending the Secret Components and Repair Techniques for Packaging Machine Upkeep
Efficient maintenance of packaging makers depends upon a comprehensive understanding of their essential components, consisting of the frame, drive system, and securing systems. Recognizing common upkeep issues, coupled with the execution of preventative methods and troubleshooting strategies, can significantly boost maker reliability. In addition, the option of repair work practices, consisting of making use of OEM parts and the importance of qualified technicians, plays an essential duty in lessening downtime. To truly grasp the ins and outs of these systems and their upkeep, one must think about the more comprehensive implications of ignoring these important techniques.
Secret Parts of Product Packaging Equipments
Product packaging machines contain a number of crucial elements that collaborate to make certain effective and effective product packaging procedures. At the core of these makers is the structure, which gives architectural honesty and houses the numerous operating parts. The drive system, commonly a mix of gears and electric motors, facilitates the motion of components, making it possible for accurate procedure throughout the packaging cycle.
An additional vital component is the conveyor system, which transports products through different phases of the product packaging process. This is typically matched by sensors and controls that monitor the position and rate of products, ensuring synchronization and reducing errors. The filling up system is crucial for precisely dispensing the best amount of item into packages, whether in fluid, powder, or solid form.
Securing devices, including warm sealers or adhesive applicators, play a crucial role in safeguarding plans, stopping contamination and extending rack life. Additionally, labeling systems are important for giving required item information, guaranteeing conformity with regulations. Lastly, the control panel, outfitted with easy to use user interfaces, permits drivers to take care of device functions, monitor efficiency, and make adjustments as needed, making sure optimal performance and performance in packaging operations.
Usual Maintenance Problems
Effective procedure of product packaging makers depends heavily on regular upkeep to prevent common issues that can disrupt production. Among these problems, mechanical deterioration is widespread, specifically in parts like conveyors, seals, and motors, which can lead to unforeseen downtimes. In addition, imbalance of parts can lead to ineffective operation, triggering items to be improperly packaged or damaged during the procedure.
One more common maintenance concern involves the build-up of dust and particles, which can conflict with the equipment's sensors and relocating components. packaging machine repair service. This not only influences efficiency however can likewise pose security dangers. Lubrication failings can lead to increased rubbing, resulting in getting too hot and eventual element failure.
Electric problems, typically stemming from loosened links or damaged wiring, can disrupt equipment features, leading to substantial production delays. Last but not least, software program problems due to incorrect setups or obsolete programs can hinder the device's operation, requiring immediate treatment. Addressing these usual upkeep concerns proactively is important for ensuring ideal efficiency and long life of product packaging equipment.
Preventative Upkeep Techniques
Implementing preventative upkeep approaches is critical for sustaining the performance and dependability of packaging equipments. These approaches include an organized approach to upkeep, concentrating on the regular inspection and servicing of devices to preempt prospective failings. By sticking to an arranged maintenance program, operators can recognize damage on parts before they cause considerable break downs.
Crucial element of a preventative maintenance method consist of regular evaluations, cleansing, lubrication, and informative post element substitutes based upon supplier suggestions. Making use of checklists can streamline this procedure, ensuring that no crucial tasks are overlooked. Furthermore, maintaining precise records of maintenance tasks help in tracking the device's efficiency gradually, facilitating notified decision-making regarding future upkeep requirements.
Educating team on the relevance of preventative maintenance improves conformity and fosters a society of positive care. Implementing a predictive upkeep part, making use of data analytics and sensing unit technology, can additionally maximize equipment performance by anticipating failings prior to they occur.
Troubleshooting Techniques
When confronted with malfunctions or inefficiencies in packaging equipments, using organized troubleshooting methods is necessary for determining and solving problems quickly. The very first step in efficient troubleshooting is to establish a clear understanding of the maker's functional parameters and efficiency metrics. This includes examining the machine's specifications, as well as any kind of mistake notifies or codes presented.
Next, operators must carry out an aesthetic examination, inspecting for evident indications of wear, damage, or imbalance. This usually includes checking out gears, belts, Get the facts and sensing units to identify potential sources of malfunction. Collecting operational information, such as production prices and downtime logs, can also give insights right into repeating concerns.
When possible problems are recognized, using a sensible method to separate the root reason is vital. This may need screening private elements or systems in a regulated manner. Involving in conversations with operators that communicate with the equipment consistently can produce valuable comments concerning unusual habits or patterns.

Repair and Replacement Finest Practices
A detailed understanding of repair work and substitute finest techniques is vital for preserving the durability and performance of product packaging makers. Routinely assessing the problem of device elements permits for prompt treatment, preventing more considerable problems that can cause pricey downtimes.
When repairs are necessary, it is Click This Link necessary to use OEM (Original Devices Producer) parts to make sure compatibility and performance. This not only preserves the honesty of the device yet likewise promotes guarantee agreements. Additionally, it is advisable to maintain a stock of essential spare parts to assist in quick replacements and reduce operational disruptions.
For intricate repair services, engaging certified specialists with specialized training in product packaging equipment is suggested. They have the experience to detect concerns precisely and perform repair work efficiently. Recording all repair service activities and components substitutes is important for maintaining a comprehensive upkeep background, which can help in future troubleshooting.
Finally, implementing an aggressive strategy, consisting of routine evaluations and predictive upkeep methods, boosts the dependability of product packaging makers. By adhering to these best practices, organizations can make sure optimum device efficiency, lower operational risks, and prolong equipment life-span.
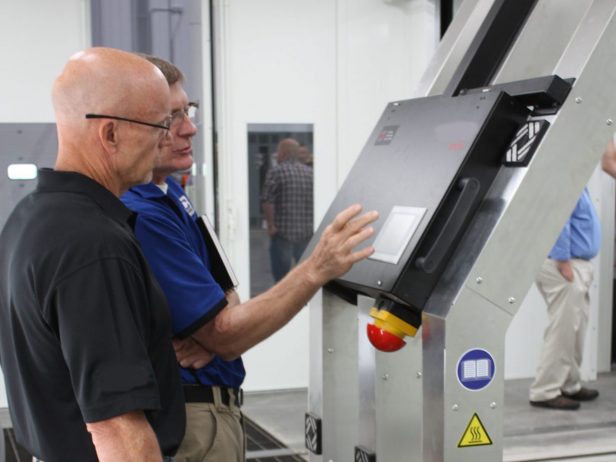
Verdict
In verdict, a thorough understanding of product packaging equipment components and effective upkeep approaches is vital for ideal efficiency. By applying these techniques, organizations can ensure the longevity and effectiveness of packaging makers, ultimately contributing to boosted functional efficiency and lowered expenses (packaging machine repair service).
Effective maintenance of product packaging makers pivots on a detailed understanding of their key components, including the structure, drive system, and securing devices.Reliable procedure of product packaging makers counts greatly on routine maintenance to avoid typical issues that can interfere with manufacturing.Executing preventative maintenance techniques is vital for maintaining the effectiveness and reliability of product packaging devices. Additionally, maintaining exact records of upkeep tasks aids in tracking the machine's performance over time, helping with informed decision-making regarding future upkeep requirements.
